Cold storage and warehouse environments are stretched to piece together the necessary labor and space to keep up with surging demands. Inherently, it’s become even more imperative that lift truck technologies optimize the productivity of the labor that operations do have on hand, as well as maximizing space by going vertical.
“New technology and products are certainly interesting, but how such advances allow the industry to redesign and rethink their processes is the most exciting thing happening right now,” said Bill Pedriana, CMO of Big Joe Forklifts. “There are new generations of order pickers, as one example, such as multi-purpose elevating platforms (MPEPs) which were developed for broken case picking in ecommerce that have tremendous potential for use in cold environments. Such machines can support new order picking strategies that require a huge number of SKUs to be stored in a small space, in operations such as urban distribution centers.”
As operations are working to maximize productivity at every turn, maintaining a strict focus on lift truck best practices and facility-specific traffic rules can be a challenge.
An advanced operator assist system (OAS) can provide a wealth of information to operators. For example, real-time location and proximity data can be used to prevent equipment from entering designated pedestrian-only zones, automatically reduce truck speed when cornering for stability, implement hydraulic arrest to prevent lifting and carrying loads that exceed weight limits and more.
Warehouses are capitalizing on their existing footprint by building up, converting otherwise unused cubic space for more storage by deploying reach trucks capable of servicing second and third level storage locations.
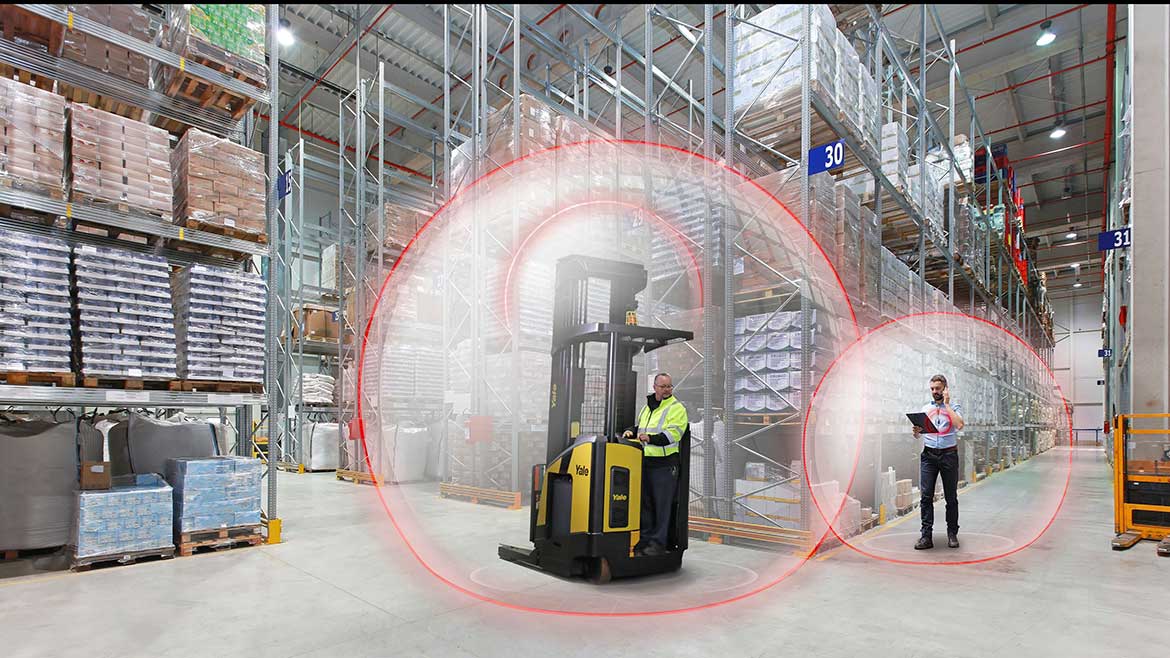
The increasing use of cloud-based telematics on lift trucks allows users to gather data “from the bottom up and get so much more knowledge about their material flows,” Pedriana said. “As we continue to make warehouse vehicles “smart” it can really be transformative if operations make the effort to focus on things that are often a bit under the radar within most operations KPIs. Mitigating bottlenecks and other hidden waste by having a true full system level view of material flows is so important in a cold environment with temperature-sensitive product.”Robots as a service – RaaS – are expected to offer flexibility for small companies though subscription and rental services, with daily or monthly rates.
As opposed to having to do lengthy site surveys, complicated ROI calculations, and expensive implementations, this technology is “going to flip to where the machines become so simple to deploy and low cost that the user becomes their own integrator and these items become a practical day to day tool for most companies,” Pedriana said.
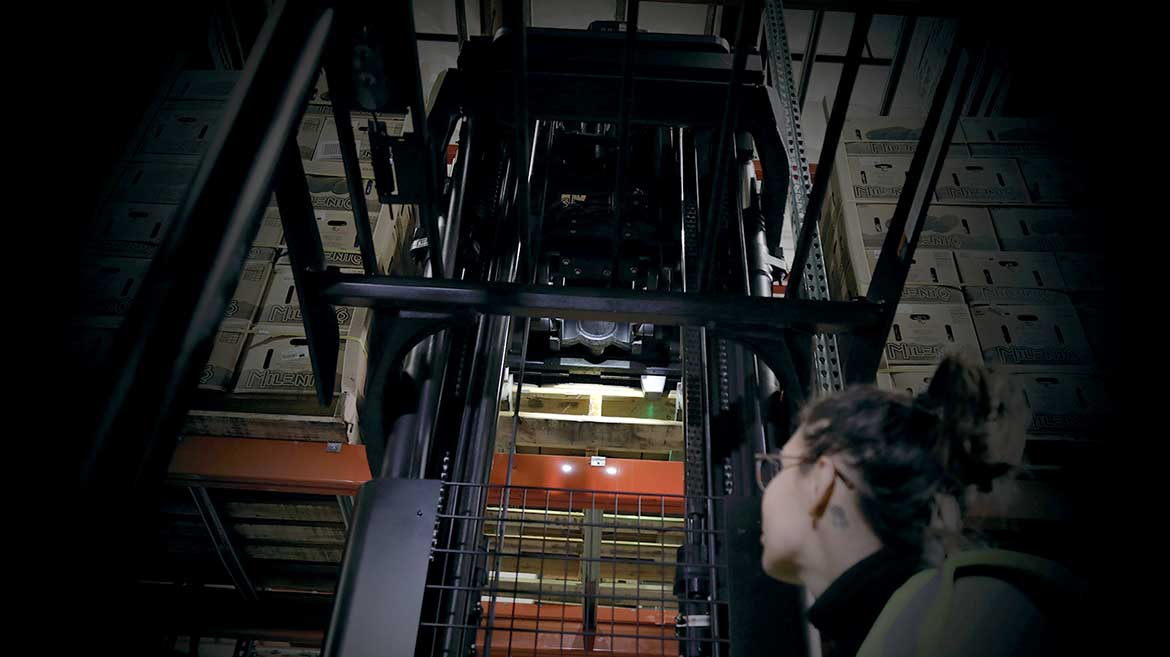
Cold Concerns
One effect of operating in such challenging environments is a frequent buying cycle.
“Cold and frozen food operations typically replace 10-12% of their lift truck fleet annually,” said Gijo George, director, major accounts, Yale Materials Handling Corporation.
The standard narrow aisle reach truck is designed for temperatures from 32 to 120 degrees Fahrenheit, but freezer/cooler packages are available that extend this range from 0 to 120 degrees Fahrenheit while subzero packages are rated for temperatures as low as -40 degrees Fahrenheit. Both include additional heaters, special fluids and lubricants required for working in extreme environments.
Lithium-ion battery-powered lift trucks, which charge up to twice as fast and stay charged longer than lead-acid battery-powered trucks, are helping drivers meet delivery schedules.
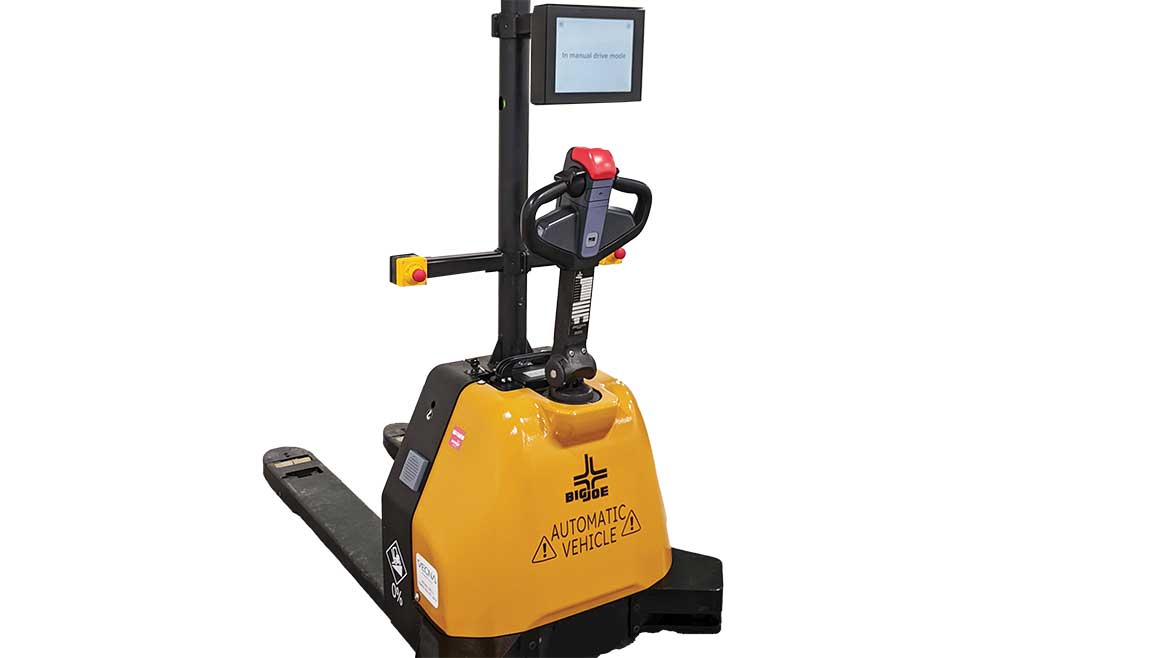
“Lithium-ion batteries are a strong choice for cold temperature food handling operations. As an electric motive power source, they do not produce emissions like internal combustion engines do, but unlike other electrification options, they can operate in a broad temperature range, from -40 to 113 degrees Fahrenheit,” George said.In addition to faster charging, they allow for smaller form factor machines to be designed for such applications.
The increasing use of cloud-based telematics on lift trucks allows users to gather data “from the bottom up and get so much more knowledge about their material flows,” Pedriana said. “As we continue to make warehouse vehicles “smart” it can really be transformative if operations make the effort to focus on things that are often a bit under the radar within most operations KPIs. Mitigating bottlenecks and other hidden waste by having a true full system level view of material flows is so important in a cold environment with temperature-sensitive product.”
Robots as a service – RaaS – are expected to offer flexibility for small companies though subscription and rental services, with daily or monthly rates.
As opposed to having to do lengthy site surveys, complicated ROI calculations, and expensive implementations, this technology is “going to flip to where the machines become so simple to deploy and low cost that the user becomes their own integrator and these items become a practical day to day tool for most companies,” Pedriana said.